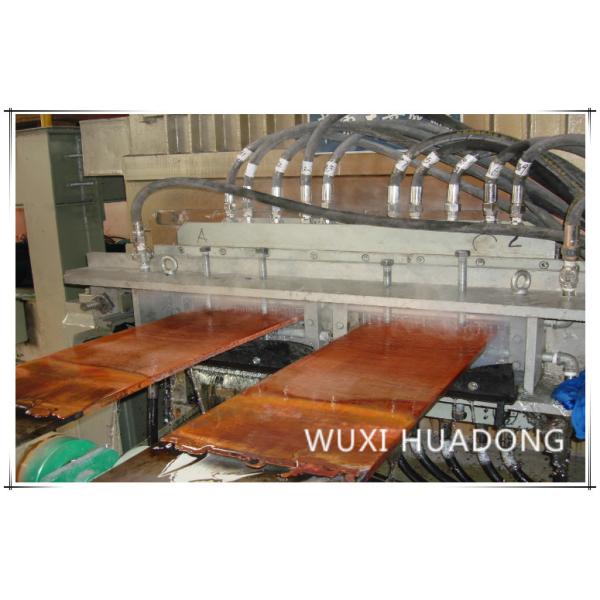
Plant Factory Horizontal Copper Strip making Continuous Casting Machine
Product Description:
Plant Factory Horizontal Copper Strip making Continuous Casting Machine is mainly used for brass/bronze bar,brass/bronze tube making.The materials can be pure brass/bronze ,scrap brass/bronze and other brass/bronze materials.
Main composed parts :
1.Induction furnace
2. Traction machine
3. Automatic cutting machine
4. peeling machine(barking machine)
5. Electric control system
6.Water cooling system
7. Dust removal equipment.
Plant Factory Horizontal Copper Strip making Continuous Casting Machine
Main technical parameters:
1. Casting speed: 1~30ton/day
2. Strip size: 150mm~650mm (width)
10mm~30mm(thickness)
3. Furnace part:
Plant Factory Horizontal Copper Strip making Continuous Casting Machine
Model | Melting rate | Mini. melting capacity | Power | Rated voltage | Rated freq. | Phase | Operation temperature | Power consumption (of melting) | Cooling water pressure | |
Melting | Holding | |||||||||
T/h | T | Kw | Kw | V | HZ | oC | Kw.h/T | Mpa | ||
GYT-200 | 0.2 | 0.15 | 60 | 30 | 380V/50Hz, or as required | 3 | 1250 | 300 | 0.2-0.4 | |
GYT-300 | 0.3 | 0.2 | 90 | 45 | 280 | |||||
GYT-500 | 0.5 | 0.3 | 120 | 55 | 260 | |||||
GYT-750 | 0.75 | 0.5 | 180 | 70 | 260 | |||||
GYT-1000 | 1 | 0.55 | 240 | 70 | 260 | |||||
GYT-1500 | 1.5 | 0.6 | 360 | 95 | 240 | |||||
GYT-2000 | 2 | 0.7 | 480 | 120 | 240 | |||||
GYT-3000 | 3 | 0.85 | 720 | 160 | 230 |
Plant Factory Horizontal Copper Strip making Continuous Casting Machine
The process diagram:
1.PROCESS
Main equipments of production line
melting furnace, holding furnace, mold, micro-travel reversible
casting machine, synchronizing shearing machines * 2, winding
machines* 3, hydraulic unit, cooling unit, and electromechanical
control unit etc.
* 1.1 For casting of pure metal or special requirements, subsurface
channel-type smelting-holding combination furnace or controllable
channel-type smelting-holding combination furnace can be adopted;
* 1.2 For producing round-shaped, tubular-shaped and special-shaped billets, cut-to-length synchronizing sawing machine can be adopted;
* 1.3 For producing round-shaped, tubular-shaped and special-shaped billets, the material stock platform for receiving and storing billets can be adopted.
2.MAJOR TECHNICAL PARAMETERS OF EQUIPMENT
1.1 | Casting speed: | |
Traction speed | 0-64 mm/s (Stepless adjustable) | |
Backstepping speed | 0-64 mm/s (Stepless adjustable) | |
Strip optimum line speed | 90-120mm/min | |
1.2 | Equipment power: | |
Combination furnace: Smelting Holding | 500Kw 200Kw | |
Traction machine | 7.5Kw | |
Hydraulic shear stress | 80T | |
1.3 | Shear thickness | 20mm(max) |
1.4 | Coiling machine parameters | |
Coiling weight | 6000Kg | |
Inside Diameter of Coil | Φ500-800mm | |
Coil diameter | 1600mm | |
1.5 | Machine noise value | Less than 85 dB |
1.6 | Height of machine operation line | +1000mm |
1.7 | Machine drive direction | Right drive |
1.8 | Production capacity | |
2 Strands: 750-1200Kg/h | width: 470mm thickness: 25mm | |
Equipment assembly machine power | 700Kw |
3. MAIN PROCESS PARAMETERS
1 | Output | 750-1200Kg/h |
2 | Temperature regulating range | ≤1300℃ |
3 | Temperature control precision of thermal insulation furnace | ±5℃ |
4 | Vertical and horizontal tolerance | Horizontal: + 0.10mm Vertical:±0.20mm |
5 | Push and pull adjustment range | Push:0-64mm/s ±0.1mm(electrodeless) Pull:0-64mm/s ±0.1mm(electrodeless) |
6 | Sickle curve | 1.5mm/m |
7 | Dragger adjustment range | Drag:0-64mm/s ±0.1mm(electrodeless) Backsteppingl:0-64mm/s ±0.1mm(electrodeless) |
8 | Drag maximum line speed | 120mm/min |
9 | Coiling adjustment range | Inside Diameter of coil Φ500-Φ800mm External diameter of coil Φ1600mm |
10 | Maximum coiling speed | 250mm/min |
11 | Elastic adjustment range | 0.95-0.75 |
12 | Tower dgree of coiliing | ≤40m |
13 | Unit power consumption | 430kWh/t |
4. EQUIPMENT PARTS LIST
No. | Equipment Name and Spec. | Unit | Quantity |
1 | Machine parts | ||
1.1 | Melting and holding combined furnace | set | 1 |
1.2 | Mould | set | 2 |
1.3 | Dragger | set | 1 |
1.4 | Hydraulic cutter | set | 1 |
1.5 | Coiling machine | set | 2 |
2 | Hydraulic system | ||
2.1 | Combined furnace titing hydraulic station | set | 1 |
2.2 | Hydraulic cutter hydraulic station | set | 1 |
2.3 | Dragger and coiling machine hydraulic station | set | 1 |
3 | Electric control system | ||
3.1 | Power frequency electric furnace control system | Set | 2 |
3.2 | Automatic control system | set | 1 |
4 | Technical documentation with equipment | set | 2 |
4.1 | Equipment installation diagram | file | 1 |
4.2 | Equipment specification | file | 1 |
4.3 | Principle diagram of electric control system | file | 1 |
4.4 | Control cabinet layout | file | 1 |
4.5 | Product specification for main electrical equipment | file | 1 |
4.6 | Hydraulic system diagram | file | 1 |
4.7 | PLC program | file | 1 |
5. AFTER-SALES SERVICE
1. The main body of the equipment will have one year of free
warranty, and special components shall be discussed separately;
2. During the trial-production period (within 3 months after
equipment commissioning is finished), our company will dispatch a
professional technician for follow-up service;
Within the warranty period, if fault occurs due to quality problem,
our company will dispatch personnel to the site to solve the
problem within 72 hours after receiving the notice;
After the warranty period of the equipment is expired, our company
will offer effective solutions within 24 hours after receiving the
notice, and will dispatch personnel for maintenance work if the
user fails to solve the problem, only charging the cost expenses.
For annual overhaul of equipment, our company will dispatch
professional technician to join the users in formulating the
turnaround plan, free of charge;
Within the warranty period, our company can dispatch professional
technician to the site to check the operation condition of
equipment and provide field service.
After the warranty period of equipment expires, one return visit
can be made on invitation once per half a year.
3. If our company has innovation and improvement points or
constructive suggestions for similar equipments, we will inform the
user in time.
Wuxi East China Furnace Co.,Ltd
Welcome to visit and inspect!
Contact person: Joey Wong
Tel: +86 510 83788308
Fax: +86 510 83786308
Mob: +86 139 2112 5611
Wechat: 86 139 2112 5611
Whatsapp: 86 139 2112 5611
email:Joey@wxhddl.cn
Joe.777@outlook.com
Wuxi Huadong Industrial Electrical Furnace Co.,Ltd.
Our company is located at the northeast of Wuxi, Jiangsu Province, with only 2.5 hours of driving distance to Shanghai Pudong International Airport, and the traffic is very convenient.
Wuxi Huadong Industrial Furnace Co., Ltd is a comprehensive enterprise integrating scientific research & development, engineering designing, system integration, equipment installation and sales & services. Our company is dedicated to professional manufacture the production lines for casting of various non-ferrous metals and heat treatment since 1989.
The production lines for casting non-ferrous metals supplied by our company is complete in categories, specifications and types, mainly capable of casting metals including copper and copper alloys, also related to non-ferrous metals such as magnesium, aluminum and zinc etc. The casting modes include horizontal continuous casting, vertical casting and upward casting; By using our production lines, customers can get billet products with sections of near-the-net-shape dimensions and shapes, including 8 major categories i.e. plates, strips, rods, foils, tubes, bars and shapes. Heat treatment equipments include multiple types of electric resistance furnaces or combination, such as well type, box type, bogie-hearth type, bell type, protective-atmosphere type, vacuum bright type, strong-convection circulation type etc. For casting production lines and heat-treatment equipments, our company can also provide various types of spare parts (furnace shells, melting grooves, water jackets, iron cores, crystallizers, special refractory, temperature measurement devices, transformers, reactors, electric resistance heating elements, and mechanical parts etc.); Our company can also provide cold-processing equipments such as drawing mills and cold-rolling mills for tubes, rods and shapes, as well as scrap metal balers etc.
Our company can develop, design, and manufacture equipments for specific production lines according to customers' requirements, provide complete services of solutions; Committed to quality, quality priority covers the whole process of designing, purchasing ,manufacturing, production, installation and after-sales services etc. We are doing our best to realized most advanced in technology, most reasonable in configuration, most superior in quality, and most inexpensive in cost. We strictly follow the requirements of ISO9000 quality system, achieving first-class product quality.
Choosing Wuxi Huadong Electric Industrial Furnace Co. ,Ltd as the
partner means choosing trust and guarantee, and the correction
choice is the safeguard for the smooth operation of your
undertakings and reliable return of your investment.
Wuxi East China Furnace Co. ,Ltd would like to
cordially welcome friends from home and abroad for visiting and
guidance.