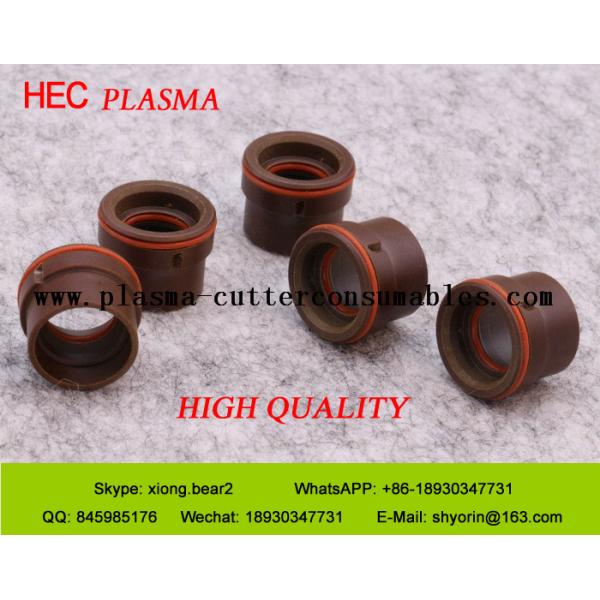
Hifocus Plasma Gas Guide .11.848.221.146 G102 For Plasma Cutting
Swirl Ring
Shanghai ZhouBo Welding & Cutting Technology company are a
professional manufacturer of plasma cutter consumables, Our company
is located in the Shanghai City, China ,it was established in
2007,but we had 10 years manufacturing experience in this field,
the new factory covers an area of more than 10000 square meters
.There are 50-100 workers and 20 research engineers.
Swirl gas cap: V4335, V4330, V4340, V4345, V4350, V4360, V4535,
V4540, V4550, V4560, Z4015, Z4020, Z4022, Z4025, Z4030, Z4140,
Z4530, Z4535, Z4545, Z4540, R4020, R4022, R4025, R4130, R4140,
R4525, R4530, R4540, G4020, G4022, G4025, G4030, G4035, G4040,
G4330, G4335, G4340, G4345, G4350, G4355
Nozzle cap: M3004, M3008, M3028, S3004, S3008, S3018, S3028, T3000,
T3030, T3045, T3145, T3060, T3160, T3208, T3209, T3219, T3228,
R3004, R3008, R3018, R3028, G3004, G3018, G3028
Protection Cap: Z501, T502, T503, V502, T522, G3209, G3219, G3249
Gas guide: Z101, Z102, Z111, Z111A, G101, G102, G121, G125
Water Tube: T901, V931, PB-S75, PB-S46/47, .11.842.601.152, G931
Machine | HEC NO. | Thum NO. | Ref NO. | Description |
| K631730 | V4330 | 11.833.101.1550 | Swirl Gas Cap 3.0 |
K631735 | V4335 | 11.833.101.155 | Swirl Gas Cap 3.5 | |
K631740 | V4340 | 11.833.101.156 | Swirl Gas Cap 4.0 | |
K631745 | V4345 | 11.833.101.157 | Swirl Gas Cap 4.5 | |
K631750 | V4350 | 11.833.101.158 | Swirl Gas Cap 5.0 | |
K631760 | V4360 | 11.833.101.159 | Swirl Gas Cap 6.0 | |
K631860 | V4560 | 11.833.111.159 | Swirl Gas Cap 6.0 | |
K42192 | T502 | 11.841.721.081 | Protective Cap Percut 370.2 | |
K42202 | T522 | 11.836.921.271 | Swirl Gas Nozzle PerCut 370.2® | |
K42201 | T521 | 11.836.901.271 | Swirl Gas Nozzle PB-S77®/PB-S80® | |
K521230 | T3030 | 11.836.901.163 | Nozzle Cap (12x1,5 30°cw) | |
K521245 | T3045 | 11.836.901.164 | Nozzle Cap (12x1,5 45°cw) | |
K521345 | T3145 | 11.836.901.1641 | Nozzle Cap (12x1,5 45°ccw) | |
K521260 | T3060 | 11.836.901.165 | Nozzle Cap (12x1,5 60°cw) | |
K521360 | T3160 | 11.836.901.1651 | Nozzle Cap (12x1,5 60°ccw) | |
K12715 | T2115Y | 11.846.921.415 | Nozzle O2 120A | |
K12720 | T2120Y | 11.846.921.420 | Nozzle O2 200A | |
K12725 | T2125Y | 11.846.921.425 | Nozzle O2 250A | |
K12727 | T2127Y | 11.846.921.427 | Nozzle O2 300A | |
K12730 | T2130Y | 11.846.921.430 | Nozzle O2 360A | |
k11025 | T2525 | .11.836.911.625 | Nozzle T2525 ArH2 280A 2.5mm | |
k11027 | T2527 | .11.836.911.627. | Nozzle T2527 ArH2 360A 2.7mm | |
k1927 | T2427 | .11.846.911.627 | Nozzle T2427 ArH2 360A 2,7mm | |
k1929 | T2429 | .11.846.911.629 | Nozzle T2429 ArH2 440A 2,9mm | |
K7244 | T104 | 11.836.921.1542 | Swirl Ring (3x0,4 cw) | |
K7241 | T101 | 11.836.921.153 | Swirl Ring (6x0,8 cw) | |
K7251 | T111 | 11.836.921.1531 | Swirl Ring (6x0,8 ccw) | |
K7242 | T102 | 11.836.921.154 | Swirl Ring (3x0,8cw) | |
K7252 | T112 | 11.836.921.1541 | Swirl Ring (3x0,6 ccw) | |
K0212 | T012Y | 11.844.921.300-AG | Silver Electrode | |
K0102 | S002Y | 11.843.021.320-AG | Cathode, Ag | |
K0112 | S012X | 11.843.121.310-AG | Cathode, Ag | |
K0122 | S042 | 11.842.411.510 | Cathode, HiFinox® (i) | |
K0132 | S052 | 11.842.511.510 | Cathode, FineFocus® (i) | |
K0221 | T051 | .11.836.911.500 | ||
K92211 | T901 | 11.844.901.152 | Cooling Tube | |
K93221 | V951 | 11.828.911.230 | Cooling Tube |
Technical Support:
How to maintain CNC cutting machine
CNC cutting machine working site and working environment is
relatively poor, relatively large metal dust. Therefore, the
machine must be fully cleaned and maintenance, the person
responsible for the equipment lubrication, maintenance and
maintenance work!
A. Safe operation:
1. CNC cutting machine is a sophisticated equipment, so the cutting
machine operation must do sanding (man, machine, posts)
2 the operator must go through professional training and be able to
skillfully operate, non professionals do not move.
3. In the operation must be confirmed without external
interference, everything is normal, the cutting plate dipping in
the cutting platform, the plate can not be more than cutting range
(Note: in hoisting to be careful).
B. Daily maintenance and maintenance:
1. Each work, must clean up the dirt and guide rail machine, make
the bed is kept clean, air and power is shut down work. At the same
time emptying machine tube with residual gas.
2 if you leave the machine for a long time to turn off the power,
in case of non professional operation.
3 observe the machine horizontal, vertical guide rail and rack
surface with no lubricating oil, to keep the good lubrication!
C. Weekly maintenance and maintenance:
1 weekly to the machine for a comprehensive clean-up, horizontal,
vertical guide rail, transmission gear rack cleaning, filling the
lubricating oil.
2 check the horizontal and vertical rail cleaning device is working
properly, if not properly and timely replacement.
3 check all the torch is loose, clean up the garbage of the
ignition gun ignition, maintain normal.
4 if there is automatic adjustment of the device, the detection is
sensitive, whether to replace the probe.
D. Maintenance of the month and quarter:
1 check the total air intake is free of garbage, each valve and
pressure gauge is working properly.
2 check all tracheal joints are loose, all pipes with no damage.
Tighten or replace if necessary.
3 check all the transmission parts are loose, check the gear and
rack meshing situation, when necessary to adjust.
4 loosen up device, drive pulley by hand, whether freely, such as
timely adjust or replace the abnormal situation.
5 check the clamping block, steel belt and guide wheel with no
loose, steel belt tightness condition, when necessary adjustment.
6 check the electrical cabinet and operation platform, the
fastening screw is loose, clean up the dust inside the cabinet with
a vacuum cleaner or hair dryer. Check if the connector is loose
(refer to the electrical manual).
7 check the performance of all buttons and select the switch, the
replacement of the damaged, and finally draw a comprehensive
detection of the accuracy of the machine.
Shanghai Zhoubo welding & cutting technology CO.,LTD.
We are a professional manufacturer of plasma cutter consumables, Our company is located in the Shanghai City, China ,it was established in 2007,but we had 10 years manufacturing experience in this field, the new factory covers an area of more than 10000 square meters .There are 50-100 workers and 20 research engineers.
In recent years, we have been sold in lots of countries and regions in Europe and Asia and gained good reputation widely with excellent quality . In order to meet customers’ requirements and improve product quality, our company has already realized mechanical processing numerical control automatization production, and been committed to manufacturing products with best quality.
Our company adopts modern management mode and devotes itself to new high performance design and production of welding & cutting equipments, with continuous technique advantages innovation .All our staff are striving to realize the aim of "Create Chinese Brand ,Build First-Class Enterprise ",with the spirit of "Being honest and pragmatic ,making pioneering efforts and seeking perfection with persistency."
Company commitment: thinking what customers think, worrying what customers worry, in time delivery and high tracking service.